The electrical system is the central nervous system of your vehicle. It orchestrates everything from ignition and fuel delivery to sensor operation and comfort features. This intricate network, comprising the alternator, battery, starter, and a web of sensors and wires, is indispensable for your car’s functionality.
As automotive technology advances, so does the complexity of vehicle electrical systems. Modern cars now feature sophisticated infotainment, digital fuel injection, and advanced driver-assistance systems, all heavily reliant on a stable electrical supply and precise communication.
Understanding Vehicle Electrical Systems: An Overview
At the heart of your car’s electrical system is the battery. It’s the initial power source, providing the energy to start the engine and run electrical components when the engine is off.
Once the engine is running, the alternator takes over as the primary power generator. It recharges the battery and powers the vehicle’s electrical systems.
The starter motor, drawing power from the battery, cranks the engine to initiate combustion and get your car running.
Beyond these core components, a network of Electronic Control Units (ECUs) and sensors manage virtually every aspect of your vehicle’s operation. From engine timing and airbag deployment to brake system management and climate control, these systems are all interconnected and reliant on a healthy electrical system.
Why Prompt Diagnosis of Electrical Issues is Crucial
Timely diagnosis of electrical problems is paramount for maintaining your vehicle’s health and safety. Electrical issues can quickly escalate, impacting performance and leading to more significant, costly repairs.
For example, a failing alternator can lead to insufficient battery charging. This can result in unpredictable breakdowns or a no-start condition. Furthermore, seemingly minor issues like battery terminal corrosion can increase electrical resistance, causing wires to overheat and potentially leading to electrical fires.
Modern vehicles, with their integrated electronic systems, are particularly vulnerable to cascading failures. A malfunction in one electrical component can trigger problems in seemingly unrelated systems. What appears as an engine performance issue might actually stem from an electrical fault.
This is where OBD2 scanners become invaluable. These tools can quickly read and interpret diagnostic trouble codes, offering vital insights into potential electrical malfunctions. Early and accurate diagnosis using an OBD2 scanner not only ensures your vehicle’s operational efficiency but also enhances passenger safety by verifying the proper functioning of all safety systems. Let’s explore how OBD2 scanners are instrumental in pinpointing electrical problems and ensuring the long-term reliability of modern vehicles.
Key Features of OBD2 Scanners for Electrical Diagnostics
OBD2 scanners are essential tools for diagnosing a wide range of automotive issues, especially the intricate electrical problems that can compromise vehicle performance and safety. These scanners are equipped with specialized features that make them highly effective in electrical diagnostics. Let’s examine these features and compare the capabilities of two popular Foxwell models: the NT710 and NT809.
Essential Features for Electrical Issue Diagnosis
- Live Data Monitoring: This feature allows technicians and vehicle owners to monitor real-time data from the vehicle’s sensors and electronic systems. By observing parameters like voltage outputs, current draw, and signal frequencies, users can identify anomalies indicative of electrical faults.
- Voltage Checks: Many OBD2 scanners are capable of measuring and displaying voltage readings across various vehicle systems. This is crucial for identifying battery and alternator issues, such as overcharging or undercharging, which can lead to significant electrical system failures.
- Data Graphing: Advanced scanners can graph live data streams over time. This is particularly useful for detecting intermittent electrical problems or fluctuations that may not be apparent during a static diagnostic check.
- Circuit Testing: Some scanners offer built-in circuit testing capabilities, allowing direct verification of circuit integrity and component functionality through the scanner interface, providing dynamic diagnostic capabilities.
- System-Specific Tests: These include pre-programmed tests for specific electrical systems such as the charging system, starting system, and battery health, all critical components of the vehicle’s electrical infrastructure.
Model Comparison: Foxwell NT710 vs. NT809
Feature | Foxwell NT710 | Foxwell NT809 |
---|---|---|
Live Data | Yes | Yes, with enhanced graphing and recording |
Voltage Checks | Basic Voltage Readings | Advanced voltage and current measurements, circuit testing features |
Bi-directional Control | No | Yes, enables active testing of components |
System Tests | Standard Electrical System Tests | Comprehensive system tests, including advanced diagnostics for complex modules |
User Interface | User-friendly, simpler navigation | Enhanced touchscreen, more intuitive and faster navigation |
Advanced Functions | Basic OBD2 functions, code reading and clearing | Advanced functions including key coding, ECU programming (model dependent), and more |
Ideal For | DIY users, basic diagnostics | Professional technicians, complex diagnostics and repairs |
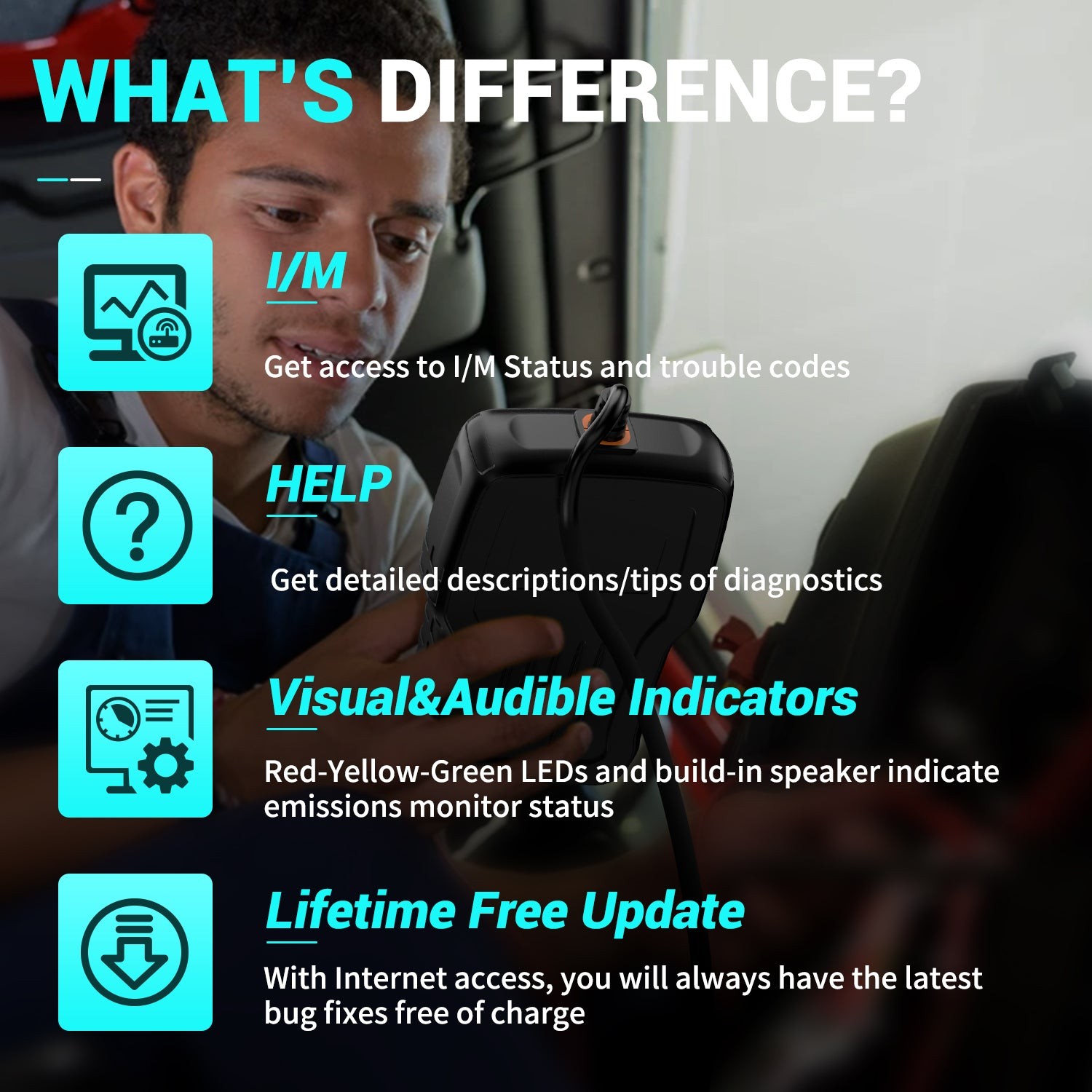

Comparative Summary:
Both the Foxwell NT710 and NT809 offer excellent diagnostic capabilities. However, the NT809 is better suited for in-depth electrical diagnostics due to its advanced features like bi-directional control, a more intuitive user interface, and faster processing. The NT809’s sophisticated capabilities make it ideal for professional use and for diagnosing complex vehicle electrical systems.
When choosing an OBD2 scanner for electrical diagnostics, consider the features that align with your diagnostic needs and the complexity of the vehicles you work on. Features like live data monitoring, voltage checks, and bi-directional control significantly simplify diagnosing and resolving vehicle electrical problems. Whether you are a professional technician or a DIY enthusiast, selecting the right tool, such as the Foxwell NT710 or NT809, depends on the diagnostic depth and complexity required for your tasks.
Step-by-Step Guide: Diagnosing Electrical Issues with an OBD2 Scanner
Using an OBD2 scanner, like the Foxwell NT710, can significantly streamline the process of diagnosing vehicle electrical problems. This step-by-step guide provides instructions on how to prepare your vehicle and effectively use the scanner for accurate diagnosis and resolution of electrical issues.
Vehicle and Scanner Preparation
Vehicle Preparation:
- Safety First: Ensure your vehicle is parked in a safe, level location. Engage the parking brake and turn off the ignition.
- Check Battery Voltage: Reliable electronic diagnostics depend on a stable power supply. Verify that your car battery is adequately charged. A weak battery can lead to false error codes or prevent the scanner from functioning correctly.
Scanner Setup:
- Software Update: Verify that your Foxwell NT710 scanner is updated with the latest software. This ensures it has the most current vehicle coverage and diagnostic capabilities.
- Familiarization: If you are new to the NT710 scanner, take time to understand its features and operation. Review the user manual to familiarize yourself with menu navigation and function locations.
Diagnostic Process: Connection to Analysis
Scanner Connection:
- Locate the OBD2 Port: The OBD2 port is typically located under the dashboard on the driver’s side. It may be near the steering column or under the dashboard, above the pedals.
- Connect the Scanner: Plug the Foxwell NT710 connector into the OBD2 port. Ensure a secure connection.
Powering the Scanner:
- Ignition ON: Turn your vehicle’s ignition to the “ON” position. Do not start the engine unless specifically instructed by a diagnostic procedure.
- Power On Scanner: The NT710 should power on automatically once connected. If not, press the power button on the device.
Navigating the Diagnostic Menu:
- Vehicle Selection: Enter your vehicle’s make, model, and year. This allows the scanner to use the correct diagnostic protocols.
- Access Electrical System Diagnostics: Navigate the scanner’s menu to find the electrical system diagnostics section. This may be under “Control Modules,” then “Body Control Module,” or directly under an “Electrical Systems” heading.
Running Diagnostics:
- Retrieve Trouble Codes: Begin by reading Diagnostic Trouble Codes (DTCs) stored in the vehicle’s computer. The NT710 will display any stored codes and provide brief descriptions of the issues.
- Monitor Live Data: Access the live data stream to observe real-time readings from electrical components and sensors. Examine voltage levels, current flow, and other relevant data that can indicate the health of electrical systems.
Data Analysis:
- Interpret Codes and Data: Analyze the DTCs and live data to pinpoint potential problems. Compare live readings to specified values in your vehicle’s service manual.
- Component Specific Checks: If the scanner highlights issues with specific components like sensors, switches, or relays, perform targeted tests such as voltage drop tests, resistance measurements, and continuity tests to further isolate the fault.
Resolution and Verification:
- Perform Repairs: Based on your diagnosis, carry out necessary repairs or replacements of faulty components or wiring.
- Clear Codes: After completing repairs, use the NT710 scanner to clear the DTCs from the vehicle’s computer.
- Re-test the System: Rerun the diagnostic scan to ensure that all electrical issues have been resolved and that no new codes are present.
Documentation:
- Record Findings: Keep a detailed record of the diagnostic process, fault codes, and repairs performed. This documentation is valuable for future maintenance and tracking recurring issues.
By following these steps, you can effectively use the Foxwell NT710 to diagnose electrical problems in your vehicle. This systematic approach ensures thorough diagnostics, helping to keep your car in optimal condition and enhancing your automotive electrical diagnostic skills.
Troubleshooting Tips Using OBD2 Data
An OBD2 scanner provides a wealth of information vital for diagnosing and resolving issues in modern vehicles. Accurate interpretation of this data is key to effective repairs and proactive vehicle maintenance. Here’s how to interpret scanner data and tips for handling common challenges like intermittent faults and error codes.
Interpreting Scanner Data for Effective Troubleshooting
Understanding Diagnostic Trouble Codes (DTCs): OBD2 scanners display DTCs, which are essential for identifying problems. Each code is standardized and points to potential issues within specific systems. For example, codes starting with “P” typically relate to powertrain issues, including engine or transmission problems.
Analyzing Live Data Streams: OBD2 scanners can display real-time data from various sensors. This includes parameters like engine temperature, RPM, oxygen sensor readings, and more. To effectively use live data:
- Establish Baseline Values: Know the normal operating ranges for each data parameter for your specific vehicle model (usually found in the service manual).
- Identify Outliers: Data readings significantly outside of normal ranges are strong indicators of a problem.
Utilizing Freeze Frame Data: Many scanners capture “freeze frame” data, which is a snapshot of sensor readings at the moment a fault code is triggered. This is incredibly helpful for diagnosing intermittent issues that may not be present during a diagnostic session.
Graphing Data Over Time: Use the graphing function on your scanner to visualize data trends over time. This can reveal patterns or anomalies that are not obvious in static data readings, especially useful for diagnosing sensor fluctuations or intermittent signals.
Addressing Common Diagnostic Challenges
Intermittent Faults:
- Inspect Grounds and Connections: Many intermittent faults are caused by loose or corroded connections or grounding issues. Check all electrical connectors for secure fit, corrosion, and damage.
- Harness Flex Test: Gently wiggle and flex wiring harnesses while monitoring live data to see if you can induce the fault to appear. This helps pinpoint wiring breaks or shorts.
- Component Stress Testing: Use the scanner to activate components (if bi-directional control is available) or monitor component performance under different conditions to reveal faults that only occur under load or specific operational states.
Error Codes (DTCs):
- Prioritize Multiple Codes: If multiple DTCs are present, address them in order of appearance, as one fault can sometimes trigger a cascade of subsequent codes.
- Consult Repair Information: Use resources like vehicle service manuals, online automotive forums, and repair databases to understand the specific context and common causes associated with each DTC.
- Clear and Re-scan: After addressing the identified issues, clear the DTCs using the scanner and then re-scan the vehicle to confirm that the fault has been resolved and no new codes appear.
General Best Practices:
- Keep Scanner Software Updated: Ensure your scanner’s software and firmware are up to date to maintain compatibility with the latest vehicle models and diagnostic protocols.
- Regular Calibration Checks: Sensors and components that require calibration (like throttle position sensors) should be checked and calibrated according to manufacturer specifications to prevent inaccurate readings and false codes.
- Document Everything: Maintain a detailed log of all diagnostic sessions, DTCs, troubleshooting steps, and repairs performed. This history is invaluable for tracking recurring problems and managing vehicle maintenance over time.
By mastering the interpretation of OBD2 scanner data and applying these troubleshooting techniques, you can significantly enhance your ability to diagnose and repair vehicle problems effectively, reducing downtime and preventing costly, unnecessary repairs. This approach ensures thorough and precise maintenance, extending the lifespan and performance of your vehicle.
Conclusion
An effective approach to using an OBD2 scanner goes beyond simply plugging in the device and reading codes. It requires a solid understanding of vehicle systems, careful data analysis, and a methodical troubleshooting process that goes deeper than superficial fixes. Each step in the diagnostic process is crucial and can be the difference between a quick, effective repair and a recurring, costly problem down the line.
Whether you are troubleshooting a complex electrical system, diagnosing engine performance issues, or performing routine maintenance, an OBD2 scanner is an incredibly versatile and powerful tool. Incorporating this tool into your vehicle maintenance routine ensures that your car remains a reliable companion on the road, ready to tackle the demands of modern driving with confidence.